第1章 デリバリー管理
1.6 全社的デリバリー管理 材料・仕掛在庫削減段階
(3)在庫形成要因マップ
工場内には、至る所に在庫を抱えているものです。しかし、キャッシュフロー向上のために「在庫量削減」を指示しても、それを改善する活動が行われないという問題が発生することがあります。勘と経験によって在庫量を管理してきた工場では、在庫が必要となる要因とその影響が定量的に把握されていません。要因が定量的に把握されていないため、どこを改善すれば良いかがわからないのです。そこで、TDMには、在庫要因の分析に使う、「在庫形成要因マップ(PSS法:Predetermined-Stock Standard)」という手法があります。
在庫形成要因マップとは、在庫を、それを構成する発生要因別の基本要素に分解し、各基本要素に対してその在庫の性質と条件に応じて定められた標準在庫量をあてはめる手法です。
在庫形成要因マップは、作業の時間研究におけるPTS法(Predetermined-Time Standard)をヒントに在庫研究の新しい手法として考案したものであり,従来の在庫の分析手法に対して次のような特徴を持っています。
・在庫量もさることながら在庫を形成する要因に意識を集中させることが
できる
・在庫形成要因の大きさが把握でき、最も在庫量の多い要因から対策を
実施することで効果的な改善活動が行える
・生産開始前,工場設計時などに,よりよい在庫量を設定することができる
・各工場,各職場に一貫した在庫標準をつくることが容易になる
・実在庫を詳しく調査しなくても分析できる
・在庫量の格付けに対する不満を取り除くことができる
図1.17は在庫形成要因マップを実施し要因の積み上げを行った例です。この結果から、生産ロットが在庫形成要因として最も大きく、次に納期未達対応であることがわかります。したがって、在庫を削減するためには、生産ロットを小さくする改善や納期達成率を向上させる施策の検討を行うことが効果的です。
このように、在庫形成要因マップは、在庫形成要因を定量的に把握するとともに、どの要因に対して重点的に対策をとるかの指針として非常に有効な手法です。
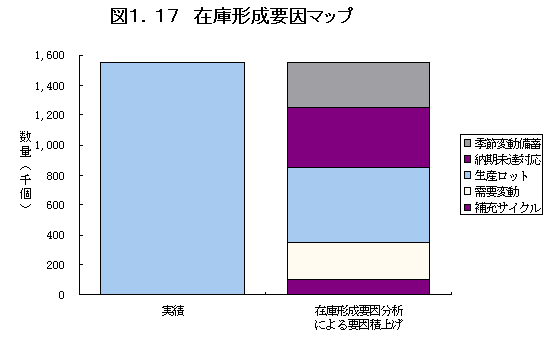
在庫の要因は多数あります。しかし次のような要因が代表的です。まず見込み生産をとっている企業の製品在庫の場合です。業務レベルが低い段階では、在庫のカウントミス、必要生産数の計算ミスによる在庫が目立ちます。返品になった不良品や、その手直し待ちの在庫が多い場合もあります。
もう少しレベルが上がると個別製品の需要変動に対応するための安全在庫、生産ロット、総需要の季節変動に対する備蓄が代表的な要因となります。見込み生産の場合、個々の製品の生産計画を立てた時点で、その需要は予測値ですから、実際に売れた数とは違います。予測値と実際の値を埋めるための安全在庫は、生産計画を立ててから製品が完成するまでのリードタイムが長くなるほど余分に必要になります。また、各種の製品は変動しながらも日々少しずつ売れるのに対して、工場では平均需要量の1週間ぶんや1カ月ぶんといったロットサイズで生産することがあります。その差で在庫が発生します。総需要に季節変動があると予測されているときに、工場の操業度を平均化するために備蓄在庫を持つことがあります。逆に工場のほうがゴールデンウイークなどの連休で減産になることに対応して備蓄在庫を持つ場合もあります。
もっとレベルアップした企業では、工場と地方の配送センターとの間のトラック輸送頻度や、輸送距離が長い場合にはその輸送期間、流通業者を含めた在庫拠点数が在庫の主要因になってきます。
仕掛り在庫もレベルが低い段階では、在庫のカウントミス・必要生産数の計算ミス・不良品・手直し待ちが重大な要因です。
レベルアップすると、トラブルに対する安全在庫、ロット差が主な要因になります。トラブルに対する安全在庫とは、自工程で、装置トラブル・品質異常が発生するかもしれないことに対応して、後工程で必要なタイミングより早く作ってしまうために停滞する在庫です。安全在庫と呼んでいますが、必要以上に持っている「安心在庫」となりがちです。またロット差とは、各工程が自分に都合のいいロットサイズで加工するために、前後工程でその差があることを意味します。それが在庫の要因となります。
さらにレベルアップすると運搬待ち、検査判定待ち、勤務差が主な要因となります。運搬待ちとは、工程間の運搬ロットあるいは運搬の頻度が停滞の原因になっていることを指します。検査判定待ちとは、抜き取り検査でサンプリングした製品を検査している間に停滞している在庫や、検査結果書などを作成する事務処理待ちで停滞している在庫です。勤務差とは、交替制で夜間や土日も稼働している工程と、日勤工程が連続している場合に、その間で発生するものです。例えば、組立てが交替制、その後の検査が日勤、梱包が交替制、出荷が日勤となっていた場合には、それぞれの間で勤務差による在庫が発生します。
材料や部品の在庫も同様にミス・不良品・ロット・運搬・検査などが在庫の要因となります。見込みで調達している材料は、需要変動に対応するための安全在庫も要因です。材料や部品に特有の要因としては、設計変更があります。設計変更で使えなくなった部品が死蔵在庫の原因になります。また投機買いも材料や部品に特有の要因でしょう。半導体などのように供給が逼迫している部品や、貴金属や石油など世界市況で決まる材料の場合、需要量を考慮するだけでなく、供給状況や市場価格を見ながら投機的に買う必要が出てきます。それがまた在庫の要因となります。
在庫は、こうした要因が重層的に積み重なった結果です。結果としては、モノが保管場所に存在しているだけにしか見えません。ですから在庫形成要因マップでその要因が見えるようにすることが必要です。